|
Last Updated
23 October, 2004
|
|
|
Back to Start
Page
1
2 3
4 5
6
7
|
|
|
Removing the 3SGTE (continued)
|
|
|
|
|
|
I think it's false economy to try to re-use a belt or hose unless you know for certain that
it's been recently replaced. When the opportunity presents itself, replacement
is cheaper in the long run. I plan to replace all of the hoses when the new motor
is installed.
|
|
|
Loosen the clamps that secure the coolant
filler hose to the coolant outlet manifold and filler neck:
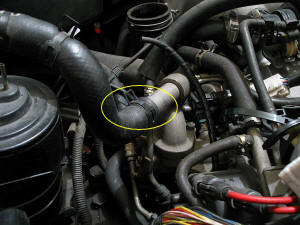
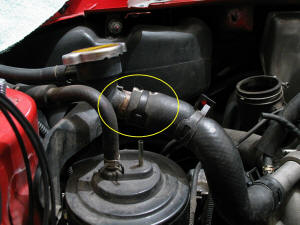
Twist the hose gently, and remove it.
|
|
|
Loosen the clamp on the radiator hose that feeds the the coolant outlet:
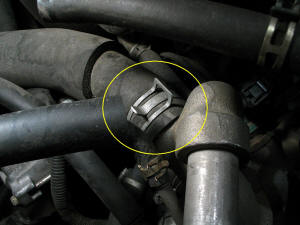
Remove the end of the hose and tie it up out of the way:
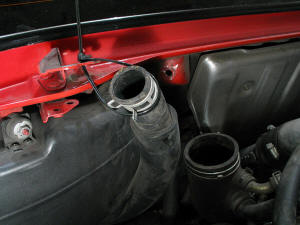
|
|
|
There's also a heater hose connected to the outlet:
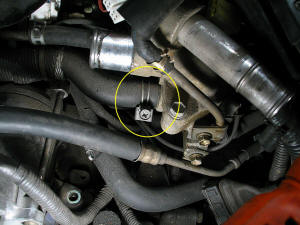
You can loosen the clamp and try to remove the hose, but mine was really stuck.
Rather than fight with it, I decided to cut both heater hoses off and remove the
pieces later. The justification is that it's faster and gentler on the hose
nipples.
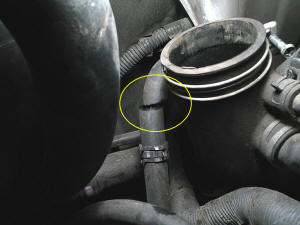
|
|
|
On the opposite side of the motor, loosen the clamp on the radiator inlet
hose...
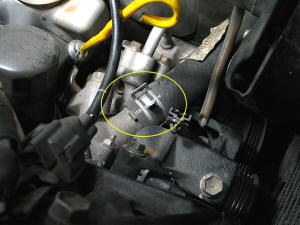
...remove the hose from the manifold...
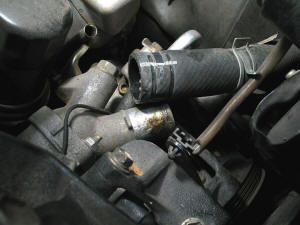
...and tie the hose end out of the way:
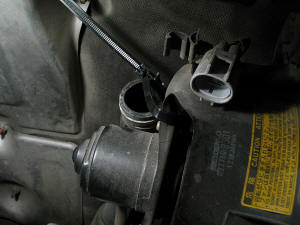
|
|
|
Clean any old gasket material completely off the coolant pipe drain bungs,
and make sure to use a new gasket or sealing washer before re-installing
the drain plugs.
|
|
|
Now it's time to jack the car up high enough to slide the engine out from
underneath. Because of the height you need to reach (about 30" of clearance at
the rear fascia), safety is a big concern. Obviously, you'll need heavy-duty
jack stands that can extend to about 24".
I raise the car a little at a time, about 2"-3", before I reset the
jack stand height. Then I raise it a bit more. I try to keep the car pretty
level, so that means moving from front to back a few times. It takes longer, but
I feel a lot safer. Of course, if you have access to a lift, then things are
much easier.
I position the jack stands just inside the lip on the rocker panels, aligned
with the jacking point marks:
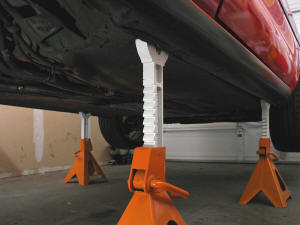
The clearance from the garage floor to the lowest edge of the rocker panel is
23½" at the rear, and maybe 2" lower in front.
The clearance to the edge of the lower rear fascia panel is 30½". Since the
motor will be rolled out the back, this is the crucial dimension. I set the
motor on a creeper, which is very low. If you use a taller dolly, you'll need to
raise the car to compensate.
Also, changing the position of the car will probably result in additional fluids
spilling out, so be prepared to catch them.
|
|
|
Remove the cotter pin from the end of the rear axle shaft:
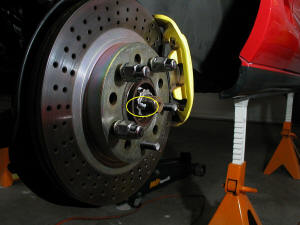
|
|
|
Remove the "cage" that fits onto the nut:
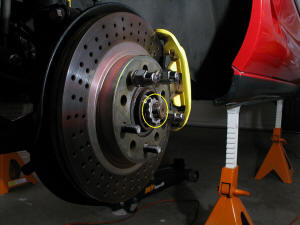
|
|
|
Getting the axle nut off is a challenge. I found that a 1¼" 6-point socket
fits fine, as I couldn't find the correct metric size (32 mm).
The folks who wrote the BGB seem to believe that simply applying the
parking brake is enough to keep the hub from turning. Maybe that works
when the car is brand new. I've never had it work for me. And putting the
car in gear and relying on the transmission to hold the axle in place
doesn't see like the correct procedure either.
Here's my approach. First, install lug nuts (I always seem to have some
old ones laying around) on three consecutive studs. Next, find yourself a
big crowbar and fit it as shown below:
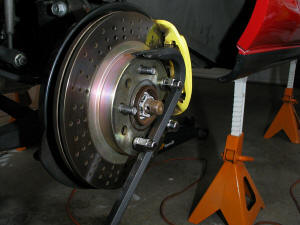
|
|
|
If the crowbar isn't long enough to reach
the ground, shim it up with a thick piece of wood, like this 4"x6" timber:
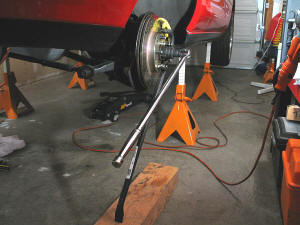
I didn't have any air tools, so I needed a long breaker bar PLUS a long
length of iron pipe. I'm always convinced the breaker bar handle will
snap, but so far it's survived. Once the nut is loose, you can remove it:
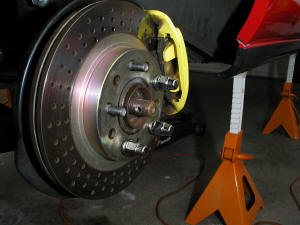
|
|
|
Since the suspension and driveshaft need to be removed, the best approach
now is to crack loose all of the mounting bolts. Most of these require
quite a bit of muscle to loosen, and it's best to apply that force before
you start removing pieces.
|
|
|
Loosen the two 17mm bolts that hold the ball joint to the hub:
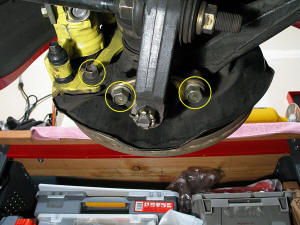
Don't remove them yet, just crack them loose so you can spin them off
easily later.
To the left of the ball joint in the photo above, you can see one of the
17mm bolts that secures the brake caliper to the hub. Loosen this bolt,
and also the top bolt which is hidden from view in this photo.
|
|
|
Loosen the 19mm bolt that secures the lower
arm to the crossmember:
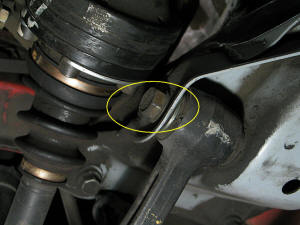
|
|
|
Loosen the 17mm through bolt that secures
the strut rod to the body. It's shown in the yellow circle below:
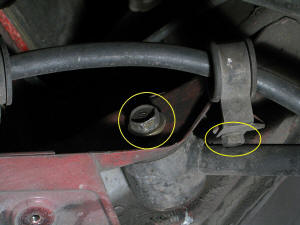
To the right of the strut rod bolt is a 10mm bolt that secures a cable
retainer for the parking brake cable. Remove the bolt.
|
|
|
There's another parking brake cable
retainer, secured with two 10mm bolts:
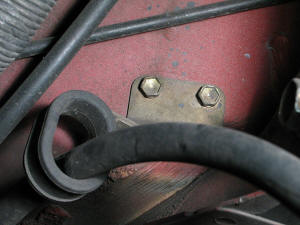
Remove those bolts as well. This provides some slack for the parking brake
cable.
|
|
|
Here's another weird Toyota engineering choice. The brake line uses a
support attached to the strut housing. However, rather than being simply
notched, the bracket has a through hole, as shown below:
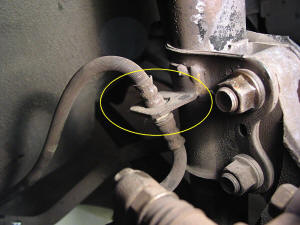
This means that in order to gain slack in the brake line you must
disconnect the line, which in turns you must bleed the brakes after
reassembly.
I had previously installed stainless braided brake lines on this car.
One of the modifications I made at that time was to cut a notch into
this bracket to enable the brake line to be freed from the bracket
without having to disconnect the line.
|
|
|
There are two clips that secure the brake line to the bracket. An "E" clip snaps
into a grove above the bracket...
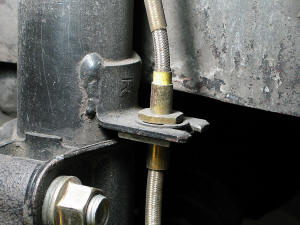
...while a "U" clip snaps in below:
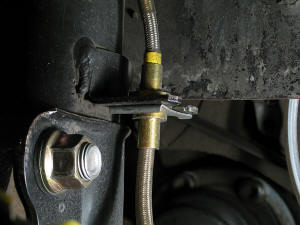
|
|
|
The "U" clip is easy to remove with a pair of needle-nose pliers:
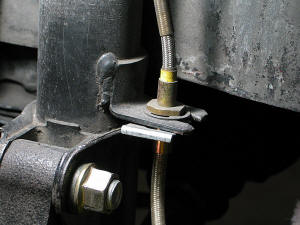
|
|
|
The "E" clip can then be pried out with a small flat-bladed screwdriver:
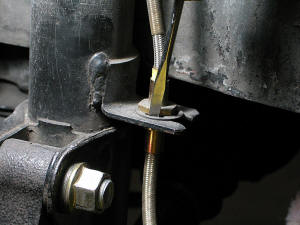
Now the brake line joint can be freed from the bracket.
If your bracket does not have a slot, you will need to disconnect the brake hose
to provide enough slack in the cable to remove the caliper.
|
|
|
Inside the wheel housing, the cable to the
ABS sensor can been seem coming through a rubber grommet, as seen below
inside the large yellow cirlce:
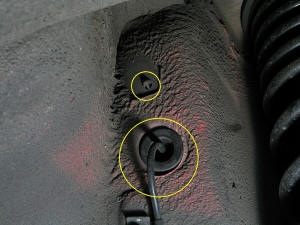
In the smaller circle is the backside of the cable retainer. Squeeze the
tabs together to free the retainer, and push the retainer through the hole
to the engine compartment.
Using a small flat-bladed screwdriver, pry the grommet towards you, until
you can pull the grommet, with its cable, through the hole. Keep this
cable out of harms way by tying it to the hub.
|
|
|
Continued on next page... |
|
|
|
|
|
Back to Start
Page
1
2 3
4 5
6
7
|
|
|
|
|